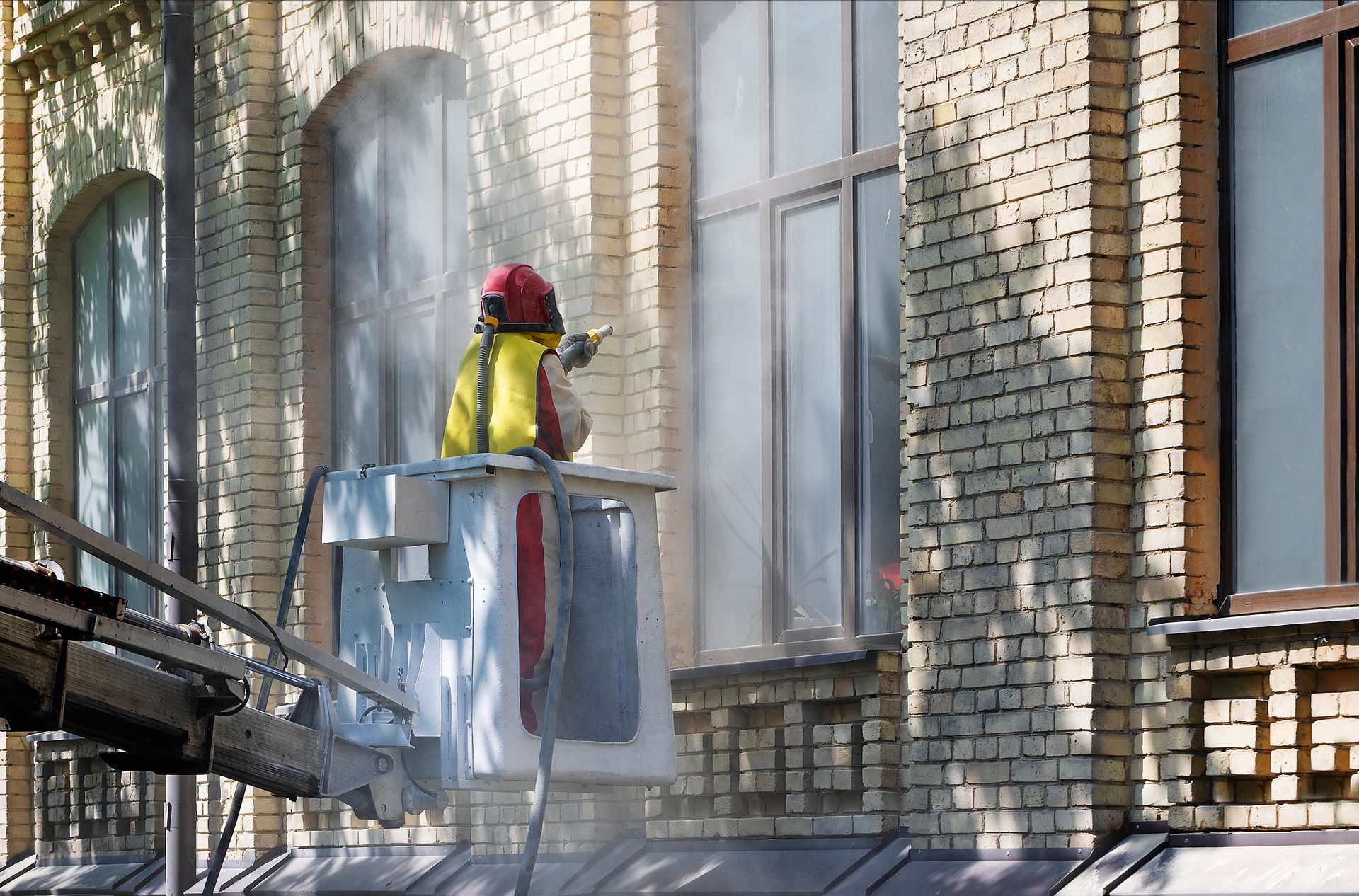
SBS Mobile Sandblasting, Shot Blasting Services In Bedford, Bedfordshire
Sandblasting and shot blasting are essential processes for maintaining and restoring surfaces to their former glory. If you're located in Bedford, Bedfordshire, and need reliable blasting services, SBS Sandblasting has been the go-to choice for over 20 years. Let's explore why sandblasting is a cost-effective solution, the different types of grit used, and what sets SBS apart from the rest.
​
The Importance of Sandblasting
Surface Restoration
Sandblasting is invaluable in restoring surfaces to their original condition. Over time, surfaces accumulate dirt, rust, and old paint, diminishing their appearance and functionality. Sandblasting efficiently removes these contaminants, revealing a pristine surface beneath. This restoration process is essential in preserving the integrity and longevity of various materials, whether it's an antique car or a historic building facade.
​
Versatility Across Materials
The versatility of sandblasting makes it applicable to a wide range of materials. From metals and wood to concrete and brick, sandblasting can be tailored to suit different substrates. The choice of abrasive and technique can be adjusted to ensure optimal results without compromising the material's structural integrity. This adaptability makes sandblasting a preferred method for diverse industries, including construction, automotive, and manufacturing.
​
Cost-Effectiveness
Sandblasting is not only effective but also cost-efficient. The process significantly reduces labor time compared to manual cleaning methods. By swiftly removing layers of rust, paint, and other debris, sandblasting cuts down on the need for multiple cleaning processes. This efficiency translates into lower costs, making it an attractive option for both small and large-scale projects.
​
How Does Sandblasting Work?
Sandblasting, also known as abrasive blasting, is a technique used to clean, smooth, or shape a surface by blasting it with abrasive material. The process involves propelling a stream of abrasive material, such as sand or grit, at high speed to remove paint, rust, or other surface contaminants. This method is effective for a variety of materials, including metal, concrete, and wood.
​
The Mechanics of Sandblasting
The sandblasting process involves several key components working in harmony. At its core, a high-pressure air compressor propels the abrasive material through a nozzle at high speed. This forceful expulsion ensures that the abrasive effectively strikes the surface, dislodging contaminants. The choice of nozzle size and shape can influence the precision and coverage of the blast, allowing for both broad and detailed work.
​
Safety Considerations
While sandblasting is effective, it requires strict adherence to safety protocols. The high velocity of the abrasive material poses risks to operators and the environment. Personal protective equipment (PPE), such as helmets, gloves, and respiratory masks, is essential to safeguard against inhaling dust and debris. Additionally, proper ventilation and containment measures must be implemented to protect the surrounding area from contamination.
​
Equipment and Techniques
Modern sandblasting relies on advanced equipment to achieve optimal results. Portable sandblasters are versatile for on-site projects, while cabinet sandblasters offer controlled environments for smaller items. Techniques such as wet blasting can be employed to minimize dust and heat, making it suitable for delicate surfaces. Choosing the right equipment and technique is crucial in achieving the desired finish and efficiency.
​
Does Sandblasting Remove Rust?
Absolutely! Sandblasting is one of the most efficient ways to remove rust from metal surfaces. The abrasive materials strip away the rust, leaving the surface clean and ready for further treatment, such as priming and painting. This method not only restores the appearance of the metal but also helps in preventing future corrosion.
​
Rust Removal Efficiency
Rust removal through sandblasting is renowned for its efficiency. The abrasive action effectively breaks down rust layers, exposing the clean metal beneath. This rapid removal process significantly reduces the time needed to prepare surfaces for subsequent treatments, such as painting or sealing. The thorough cleaning ensures that no rust residue remains, which could otherwise compromise the new coating's adhesion.
​
Surface Preparation for Priming
After removing rust, sandblasting prepares the metal surface for priming. The roughened surface created by the abrasive action provides an ideal texture for primers to adhere to. This adhesion is crucial in forming a protective barrier against future corrosion. Proper surface preparation through sandblasting ensures that the subsequent coatings are both durable and aesthetically pleasing.
​
Prevention of Future Corrosion
Beyond immediate rust removal, sandblasting plays a role in long-term corrosion prevention. By completely stripping away rust and contaminants, the process halts the progression of corrosion. Combined with subsequent protective coatings, sandblasting extends the lifespan of metal structures and components. This preventative measure is especially valuable in industries where metal durability is critical.
​
Different Types of Grit Used for Sandblasting
Different projects require different types of grit, each with its own unique properties. Here are some common types:
​
Glass Beads
Ideal for achieving a smooth finish without damaging the surface, glass beads are popular in delicate applications. They are especially useful in automotive and aerospace industries, where a gentle touch is required to avoid surface deformation. The round shape of glass beads provides a peening effect, enhancing the surface's fatigue resistance while maintaining a smooth texture.
​
Aluminum Oxide
A popular choice for its hardness and ability to clean surfaces quickly, aluminum oxide is versatile across various applications. Its sharp edges allow it to cut through tough coatings and rust with ease. This abrasive is frequently used in industrial settings where efficiency and durability are paramount, making it ideal for preparing surfaces for painting or sealing.
​
Steel Grit
Used for cleaning metal surfaces and preparing them for coating, steel grit is a robust abrasive. Its angular shape makes it highly effective in removing tough residues and creating a textured surface for coatings to adhere to. Steel grit is preferred in applications requiring aggressive cleaning and surface preparation, such as shipbuilding and heavy machinery maintenance.
​
Plastic Abrasives
Perfect for delicate surfaces where minimal damage is required, plastic abrasives offer a gentle cleaning solution. They are often used in industries like electronics and aerospace, where precision and care are essential. Plastic abrasives can remove coatings without harming underlying materials, making them suitable for sensitive applications.
​
Wet Blasting vs. Dustless Blasting
Both wet blasting and dustless blasting are variations of traditional sandblasting, offering unique benefits:
​
Wet Blasting
Wet blasting involves mixing water with the abrasive to minimize dust and reduce heat generation. This method is ideal for surfaces sensitive to heat or static electricity. The addition of water not only suppresses dust but also cools the surface, preventing thermal damage. Wet blasting is often chosen for applications involving sensitive equipment or in environments where dust control is critical.
​
Dustless Blasting
Similar to wet blasting, dustless blasting incorporates water but with added benefits of dust suppression and environmental friendliness. It's perfect for projects in populated areas where dust control is a concern. The reduction in airborne particles makes it a safer option for operators and bystanders. Additionally, the water acts as a lubricant, reducing abrasive wear and extending equipment life.
​
Choosing the Right Method
Understanding these methods helps in selecting the appropriate technique for your project needs. Factors such as the material being treated, environmental considerations, and desired finish all play a role in deciding between wet and dustless blasting. Consulting with a professional can ensure that the chosen method aligns with the project's specific requirements, achieving optimal results.
​
Why Choose Us?
Choosing the right service provider is crucial for the success of your project. Here's why SBS Sandblasting stands out:
​
Over 20 Years of Experience
With decades of expertise, SBS Sandblasting has honed its skills and techniques to deliver exceptional results. Our long-standing presence in the industry is a testament to our reliability and commitment to quality. Clients benefit from our wealth of knowledge and proven methodologies, ensuring projects are completed efficiently and effectively.
​
Cost-Effective Solutions
We offer competitive pricing without compromising on quality, ensuring value for money. Our streamlined processes and efficient techniques minimize labor costs, passing savings onto our clients. By choosing SBS, customers can expect premium services that align with their budgetary constraints, making high-quality sandblasting accessible to all.
​
Up To Date Equipment
Our use of advanced machinery allows us to handle projects of all sizes efficiently. Whether it's a small residential job or a large industrial undertaking, our equipment is equipped to meet diverse demands. The incorporation of cutting-edge technology ensures precision, speed, and safety, enhancing the overall quality of our services.
​
Highly Skilled Team
Our professionals are trained to tackle various challenges, ensuring your surfaces are treated with care and precision. Continuous training and development keep our team at the forefront of industry standards and practices. This expertise translates into exceptional customer service and results that consistently exceed expectations.
​
Priming After Sandblasting
After sandblasting, priming is a crucial step to ensure the longevity of the treated surface. Priming creates a protective layer that prevents rust and provides an ideal base for painting or other coatings. At SBS Sandblasting, we offer comprehensive services that include priming, ensuring your project is completed to the highest standards.
​
The Role of Priming
Priming serves as the foundation for subsequent coatings, enhancing their durability and appearance. By forming a strong bond with the surface, primer ensures that paint or sealants adhere properly, reducing the risk of peeling or chipping. This step is vital in achieving a flawless finish and extending the lifespan of the treated material.
​
Protective Barrier Against Corrosion
Primers act as a shield against environmental factors that can cause corrosion. By sealing the surface, they prevent moisture, oxygen, and other corrosive elements from reaching the material. This protection is crucial in maintaining the integrity of metal surfaces, particularly in harsh or humid environments.
​
Customizable Priming Solutions
At SBS Sandblasting, we offer customizable priming solutions tailored to your specific needs. Whether it's a metal, wood, or concrete surface, our range of primers ensures optimal protection and preparation for further treatments. By choosing the right primer, we guarantee that your project receives the best possible care from start to finish.
​
The Cost-Effectiveness of Sandblasting
When considering surface preparation methods, sandblasting is often the most cost-effective choice. Its efficiency in removing rust, paint, and other contaminants reduces labor time and the need for additional cleaning processes. Moreover, by extending the life of your surfaces, it saves on future maintenance costs.
​
Reducing Labor and Time
Sandblasting significantly cuts down on labor and time compared to traditional cleaning methods. The rapid removal of contaminants streamlines the preparation process, allowing projects to progress swiftly. This efficiency translates into reduced labor costs, making sandblasting an economical option for both small and large-scale undertakings.
​
Minimizing Additional Cleaning
The thoroughness of sandblasting eliminates the need for multiple cleaning stages. By effectively removing all debris in one pass, sandblasting reduces the necessity for follow-up cleaning processes. This minimization of steps not only saves time but also conserves resources, further enhancing the cost-effectiveness of the method.
​
Prolonging Surface Lifespan
By thoroughly cleaning and preparing surfaces, sandblasting extends their lifespan. The removal of corrosive elements prevents further degradation, ensuring that surfaces remain in optimal condition for longer. This longevity reduces the frequency and cost of future repairs or replacements, offering long-term savings for property owners and managers.